BROOKE FEDDER | MECHANICAL OPTION
DR. WILLIAM BAHNFLETH
UNIVERSITY OFFICE BUILDING
MID-ATLANTIC REGION
Building Statistics Part i
General Building data, Architecture, Building Envelope, and Sustainability
GENERAL BUILDING DATA
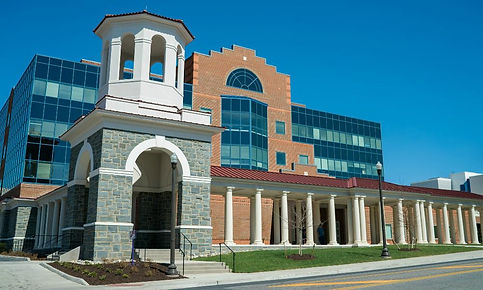
As per the wishes of the building owner to remain anonymous, this building will be referred to as University Office Building located in the Mid-Atlantic Region.
coNFIDENTIAL
General INformation


Primary Project Team
Architecture
This project is meant to repurpose a hospital, specifically a cancer center, into office spaces for a University. The hospital conversion includes a combination of office, reception, meeting and presentation spaces. The nuclear medicine area is repurposed into a Radiation Laboratory for use of the University. The scope of renovations included repairs to the exterior envelope, glazing replacements, interior layout modifications, increase in accessibility where possible, as well as a complete MEP, telecommunication system, life safety, fire alarm and security system replacement.
Major National Codes

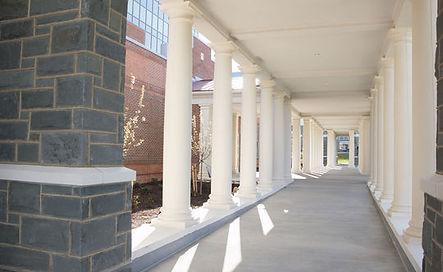
The specific state for which these codes apply will be kept confidential, as well as the zoning for this project. Also note the university has historical guidelines to be upheld.
Building Enclosure
After an exterior façade study was conducted, the enclosure was reconstructed as necessary. The original construction was composed of brick, rigid insulation, and insulated windows. A curtain wall is present on the majority of the building. In contrast, the mechanical penthouse was constructed with concrete masonry units with a brick veneer. As per the exterior envelope study, the windows were replaced to be more UV friendly and repairs were made to the brick veneer and CMU walls as needed.
Facade
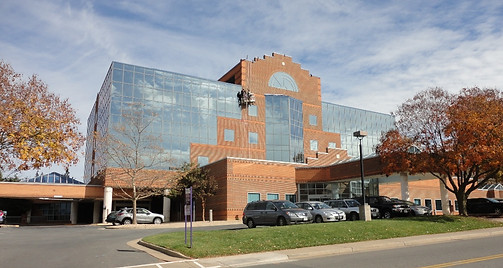
Roof
The roof is constructed of metal decking with steel W section roof structure, which includes fire proofing. It is held by varying sizes of concrete columns, a minimum of twelve inches, per existing construction drawings. Two skylights are also present within the building.
Sustainability Features
The design goal is to reach LEED Silver level, between 50 to 59 points according to the LEED Green Building Rating System for New Construction Version 3, 2009 Edition.
Building Statistics Part Ii
Primary Engineering Systems & Engineering Support Systems
Construction Management
This adaptive reuse project renovated a 69,271 gross square foot hospital for use as an office building for a university. With W.M. Jordan Company as the general contractor, the original budget for this design-bid-build project was $14.5 million, but the final bid was $18.6 million. Substantial completion was achieved in spring 2017, on schedule, after 16 months of construction and was open for use for the Fall 2017 semester.
mechanical
The original hospital was served by four air handling units located in the mechanical penthouse. These packaged units ranged from 15,000 to 20,750 CFM each. The existing system was largely demolished with the exception of the natural gas-fired boiler and its associated buffer tank, which replaced an older version only two years ago.
Two 32,000 CFM custom indoor penthouse type air handling units replace the original four. AHU-1 serves floors 1 and 2, while AHU-2 serves floors 3 and 4. A variable air volume (VAV) system distributes air via overhead air devices. These units utilize airside economizer controls for free cooling and carbon dioxide sensors to regulate the minimum requirements for ventilation air based on space occupancy. Occupancy sensors are used to reset the VAV boxes to the minimum requirements for ASHRAE 62.1 during regular occupancy hours. During unoccupied hours, the air handling units will be powered down. Fan coil units are located throughout the building to ventilate spaces when the AHU’s are powered down. Design is based on a 16 hour day, 5 days a week to allow for late night work and group meetings.
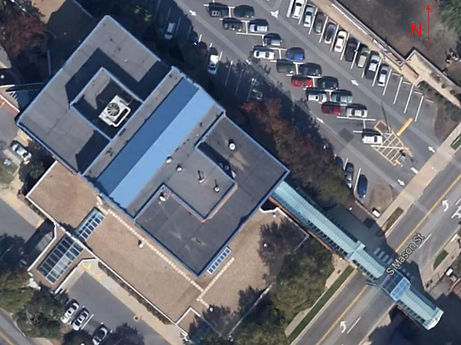
The image above shows an aerial view of the roof. The mechanical penthouse, where most of the mechanical equipment is housed, may clearly be seen.
University Office Building utilizes a chilled water system for cooling and dehumidification, provided from a dedicated stand-alone chilled water plant located in the building and in the penthouse. The heat recovery mode of this system, an air-source heat pump modular chiller, may be used for dual demand of chilled water and heating hot water when necessary. Heat rejection from chilled water generation is transferred to a heat recovery hot water loop to preheat the hot water return, providing some gas savings.
A Direct Digital Control (DDC) energy management and automatic temperature control system is provided with all HVAC equipment. This system communicates with the integrated campus automation system to regulate the following operations:
-
Start and stop functions of equipment
-
Temperature measurement and zone monitoring
-
Set point adjustment of control points
-
Equipment lead-lag
-
System occupancy and day-night operation
-
Energy consumption
Structural
University Office Building maintains the hospitals original cast-in-place concrete footings, foundations, and 6” floor slabs. Structural engineers inspected the original system and performed calculations for the covered walkway addition. Other than notes for coordination with mechanical and electrical systems, little seems to have been changed with the existing structure of this building.
Lighting/Electrical

The image above shows one of the presentation spaces where the lighting is designed for the speaker to set up at they see fit.
The existing electrical service and switchboard is maintained for University Office Building. Existing building system voltage is 480Y/277 volt and is maintained for future use. Because of this, mechanical equipment is rated for 480 volts, three phase. For small mechanical loads, receptacles, and convenience power, single phase, 120 volt power is provided. Each floor, as well as the mechanical penthouse, has its own electrical room for branch circuit panelboards and dry type transformers. Existing panelboards and dry type transformers were salvaged where possible.
Variable frequency controllers (VFCs) control motors. Motors and VFCs are placed within line of sight of their respective motors where possible. 460 volt, three phase is designated for motors rated ½ horsepower or greater, while motors rated less than this standard are 115 volt, single phase.
New interior lighting fixtures utilize energy efficient fluorescent type and light emitting diodes (LED). Ceiling or wall mounted occupancy sensors are used in areas other than lounges, corridors, and stairwells. Large conference rooms and presentation spaces are designed to incorporate zones for the speaker, whiteboard, general seating, and perimeter walls. These systems may be operated by the user at the lighting control station located in the front of the room.
Engineering Support Systems
Transportation
Telecommunications
All stairs and elevators have been designed to the most recent code. Emergency hatch for elevators and hand railings for appropriate egress have also been specified.
Telecommunication systems have been specified for the first floor, where the Vaults reside. Lab services, such as duplex data outlets and fume hoods, were designed by SST Planners. Office spaces on other floors of the building are also equipped with the necessary systems, such as phones and computers.
Fire Protection
A fire protection system was implemented based on the maximum occupancy per floor allowed by code. From this information, a full life safety egress plan was erected to ensure the number of exists are present, walls are specified with the appropriate fire rating, and egress travel paths are defined. New fire alarms and sprinkler systems were installed in each space as well.